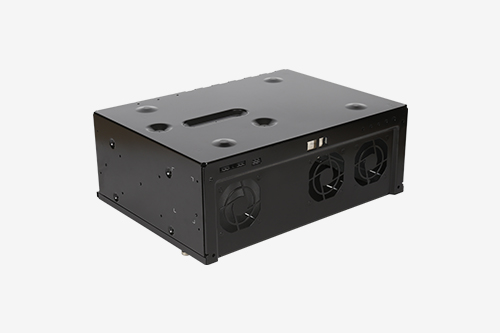
使用合适的刀具和冲压材料:根据不同的五金加工材料选择合适的刀具,使刀具与工件之间的摩擦系数动、静摩擦系数小,添加性能良好的切削液可以改善刀具和精密零件的摩擦特性。
提高机床传动系统的摩擦性能:用滚珠丝杠代替普通丝杠,用液体摩擦代替边界干摩擦,采用专用润滑油,通过提高机床传动系统的摩擦性能,提高进给系统的灵敏度,减少金属冲压件的振动现象。
提高系统的刚度:提高整个过程的刚度,可以有效地减少这种现象的发生。具体措施包括:减少刀具伸出刀架的长度,加厚刀柄,提高刀架的刚度;减小冲压件的长径比,采用中心架等中间支撑来增加工件的刚度;
增加系统的阻尼:为了增加系统的阻尼,可以选择内部阻尼较大的材料作为支撑,在零件上加入高阻尼材料进入阻尼环节,以减少振动现象。
对工件表面进行处理:例如使用电镀处理、阳极氧化、抛光加工、表面淬火等工艺,这些工艺可以改善工件的表面状态和性能,提高工件的耐磨性、耐腐蚀性和硬度等。
控制冲压过程中的温度和速度:温度和速度的控制可以影响金属冲压件的变形和表面质量。在加工过程中,应该根据材料和模具的特点控制好温度和速度。
优化模具设计:模具的设计对金属冲压件的表面质量有很大的影响。应该根据产品的要求和工艺条件优化模具设计,减少模具对金属材料的影响。
定期维护和检查:定期对机床和模具进行检查和维护,及时发现并解决潜在问题,保证设备和模具的正常运行。
推荐阅读
CNC加工件
五金加工成品件 华夫饼机
CNC加工件
不锈钢钣金加工!深圳机械加工误差是代表零件的几何参数吗
汽车五金零配件加工制造变形的预防